3D metallic printing
The use of 3D metallic printing technology in the production of tools
for car manufacturing
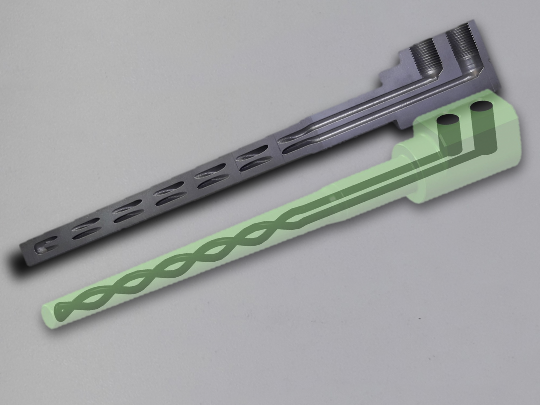
The Department of Metallurgical Tools Production (PSW-F) has created a 3D printing competence centre. This competence centre brings together members with the necessary know-how responsible for metallic printing.
The part, manufactured using PBF (Powder Bed Fusion) technology, is formed by successively applying metal powder to a construction pallet and sintering individual layers with a laser. This process is repeated until the complete part is printed.
The PBF method is used to produce, for example, parts of molds with complicated shapes of cooling channels, which may not be produced by conventional methods, or prototype parts for the needs of the development department.
3D metallic printing technology makes it possible to create a kinked or spiral hole. This is used for the production of shaped positions with conformal cooling for better cooling of aluminum die-casting molds parts. Conformal cooling shortens the solidification time of the casting in the mold and thus increases productivity in metallurgical department.
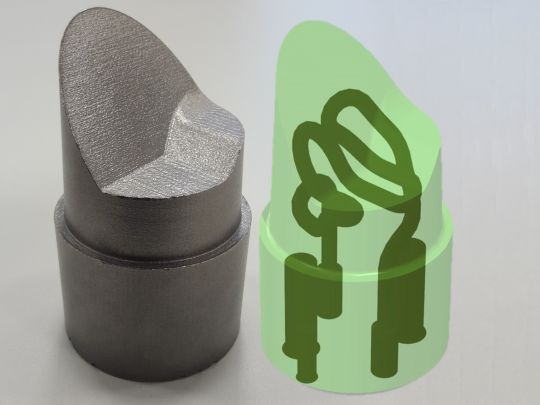
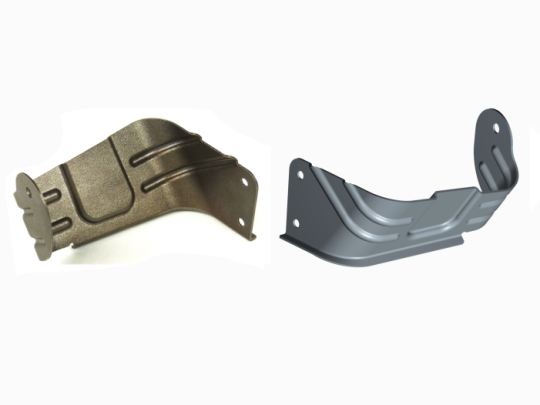
Via the web form available here, it is possible to contact the PSW-F department with a request to print your project.
An example of an already implemented project is the printing of a prototype of a headlight bracket, which the client needed to deliver in a very short time. Our colleagues from PSW-F complied with the requirements and the client received two printed parts using PBF technology within seven days of filling out the form.
Another example of 3D printing, this time made of aluminum alloy, is the prototype of the gearbox housing, on which the new bearing arrangement was tested during development.
The production of serial tools using 3D metallic printing technology is still more expensive than the technologies currently used. The use of metallic printing can move the project forward significantly, as it is possible to produce a tool that is not manufacturable by conventional methods, which can ultimately reduce the overall cost of the main production. This method is used by Škoda Auto in cooperation with other brands in the Group and externally with universities.
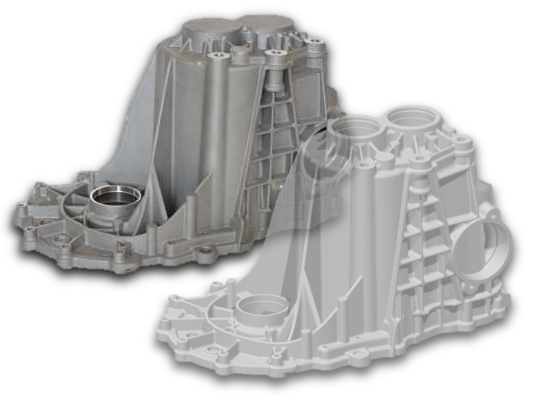
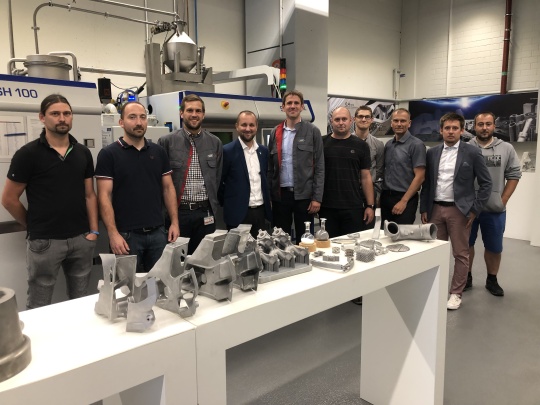
Other activities of the PSW-F unit, which are connected with this technology, are educational events. These events serve to broaden the horizons of 3D metallic printing and to transfer this experience within Škoda Auto a.s. For this purpose, colleagues regularly participate in meetings of 3D printing groups in Wolfsburg and Ingolstadt. They also participate in professional conferences where they present their results and organize internal workshops for the company’s employees in order to raise awareness of this modern technology.
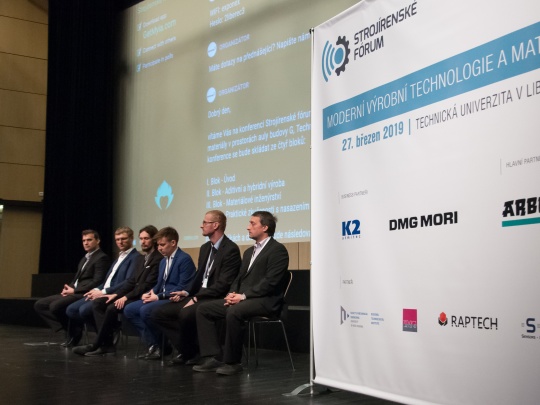
Výroba části formy pro odlévání bloku motoru aditivní metodou
The principle of printing using the PBF method can be seen in the video – it consists in the fact that fine steel granules with a diameter of 20 μm – 80 μm are applied in layers with a thickness of 50 μm and are literally “sintered” into the desired shape using a 400W laser according to a software program.
It could be compared to a machine tool, but in this case, the machining tool is not a knife, but a laser beam. Everything takes place in a protective atmosphere. It depends on the type of powder used as a raw material. The construction time of such a part depends on its size – it is in a matter of days.
What about the question of accuracy, which is so crucial for the Tool Shop?
While in some other operations the accuracy of the parts from the 3D printer is sufficient, for the extremely precise Tool Shop it is not yet, therefor all the parts are printed with an addition and are heading for final processing. However, the results are becoming more and more positive.
Another method of 3D printing is the DED (Direct Energy Deposition). The principle of DED is based on melting the material using a laser beam. The material is supplied to the melting site by a gas stream that carries the metal powder. The material molten by the beam is layered to form the desired structure.
We use DED technology for renovation of molds for engine block castings and for renovation of forging tools. To do this, we use the LaserTec125Hybrid, where a damaged tool can be repaired in one clamping in three steps. The damaged shape is milled, welded in a controlled process and then machined to the final size. The repair process is thus significantly faster and therefore cheaper.
The video shows a practical demonstration of the use of a hybrid machine in the repair of a part of a mold for aluminum die casting.
Join our team
You can find vacancies on the skoda-career.com portal. Please contact our specialists.