History of tool production
…first for the production of bicycles, later for motorcycles
and, above all, for cars.
While the development of the company, production, individual types and sporting achievements are well known, some operations and events in the company have remained on the edge of interest. Undeservedly, this also applies to the production of tools. Its operations are not in plain sight, many employees have never set foot in its halls. Even in the archives, there is no more than a few pieces of information. At the same time, the production of tools in every car manufacturer is not only crucial, but also very attractive.
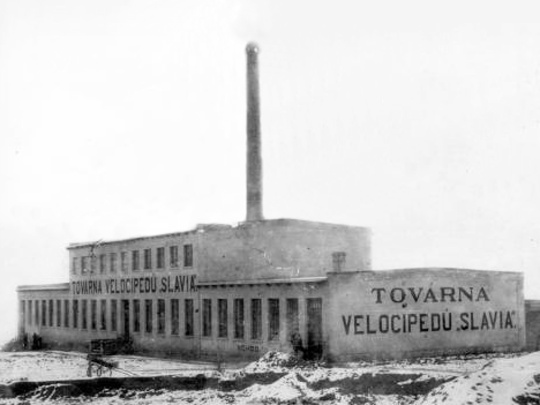
Slavia factory
In the beginning, there was a bicycle.
There is no written evidence of this, but it could not have been otherwise: the production of tools had to be introduced at the company Laurin & Klement (L&K) as early as the end of the 19th century. We conclude from this that in 1898, i.e. three years after the company was founded, the assembly of bicycles had a factory character. Mass production means mechanization, unification, division of the process into more simple steps that ensure automation, greater accuracy in repetition and guarantee of product conformity.
At the end of 1899, two L&K motorcycles under the Slavia brand were introduced in Prague. However, there were only a few customers at home, so it was necessary to acquire customers abroad. In the mid-1900s, Klement went to England, the cradle of industrial production in Europe. He succeeded with Harry Heweston, the English representative of the Benz company. Klement returned to Mladá Boleslav with an order for 150 motorcycles. They would not have been able to accept this job at all without special tools.
Allegedly, as early as 1900, toolmakers Josef Marinský and Vojtěch Dundr produced drilling templates that made production more accurate and faster. We have written documents about the production of tools, although this does not mean that there was already a separate tool factory here in 1900. Rare evidence of the existence of the Tool Shop can be found on the personnel card of Josef Horáček, who was hired on 12 May 1903 as a toolmaker. He was apparently a capable guy, because in June 1911 he was appointed foreman of the Tool Shop. In any case, photographs of the Hardening Shop, Soldering Shop and the Forge from 1905-1906 show that there can be no doubt about the production of tools at L&K at that time.
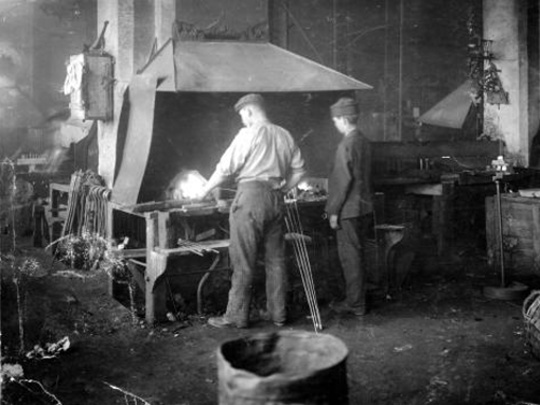
Hardening shop
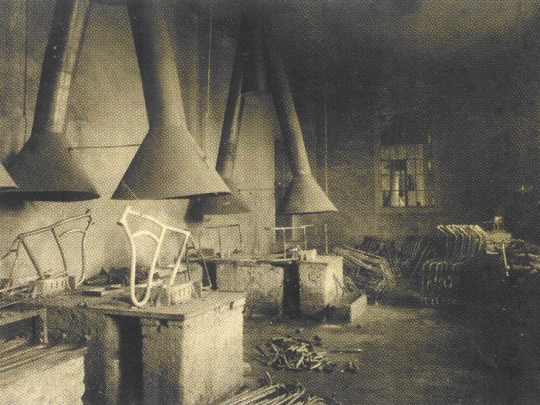
Motorcycle frames solder
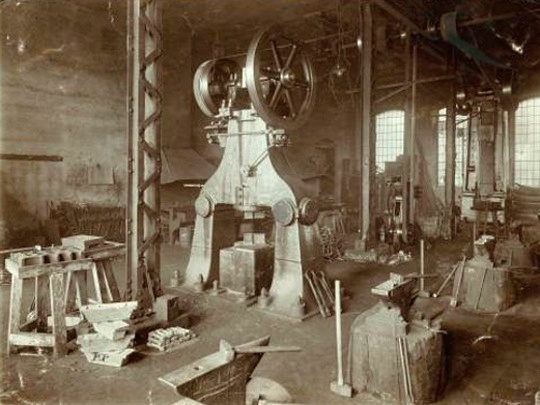
Forge

1910 – L&K factory
The start of automobile production in 1905 presented completely new challenges, especially in terms of car body. Their design was based on the construction of carriages and required mainly wheelwrights and joiners. Only the fenders and bonnet were made of sheet metal. On its sides there were slits for the removal of warm air. The fact that they are just like each other is evidence that they were make on the jig. The wooden elements of the skeleton had a variety of shapes, the correct curvature of which was checked by a number of templates. A number of parts were steamed and then bent – of course, also on tools, without which the construction of the car body would have been impossible. Spoked wheels, most often made of wood, were tightened by iron hoops, which were shaped to the required radius on the twister.
The annual report for 1908 states that the car manufacturer provides all the components of the cars produced by itself, including models and samples. The Tool Shop supplied a number of drill jigs, templates and probably also knock-out mock-ups on which fenders, for example, were shaped by hand.
In 1909, L&K purchased a license for the production of stationary engines from the Dutch company Brons in Appingedam. It was a good investment. Single-cylinder engines produced in a wide range of sizes and power were in great demand – they served as power units in factories, mills, power plants and farms. The hall for their production – Bronzák – also served as a Tool Shop, as evidenced by a photograph from 1911. As witnesses recall, the Tool Shop was preserved here even after the Second World War. Today, it houses a part of the company’s museum.
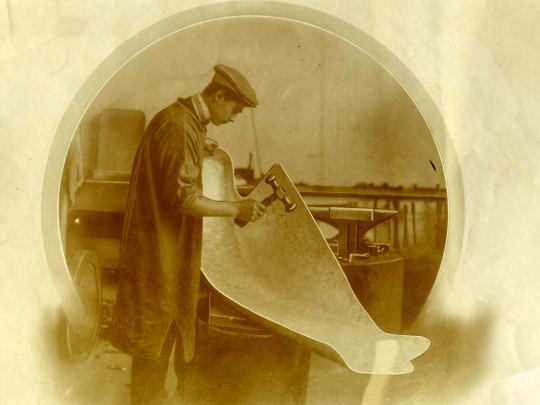
Manual fender knocking
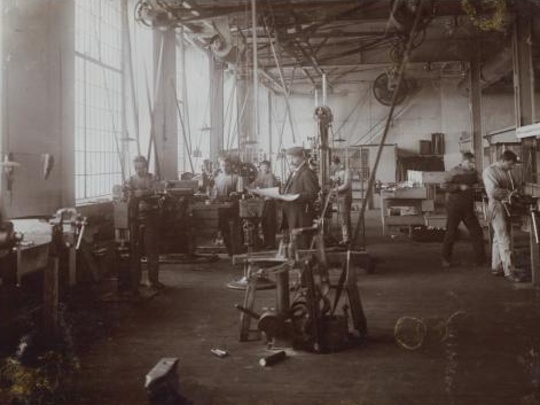
Tool shop and engine Brons manufacturing
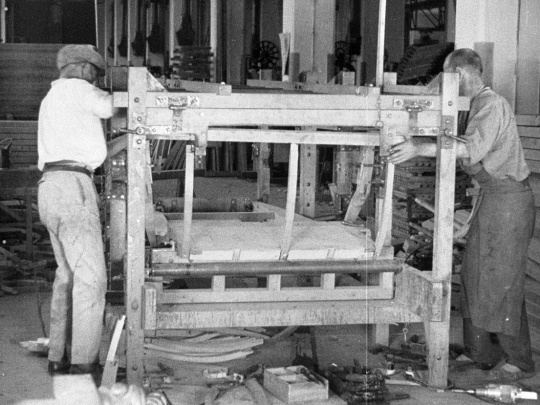
Jig for gluing bodywork
To increase production, two designers designed a number of single-purpose machines, of which 150 pieces were built by the plant’s own forces from autumn 1914 to April 1915. The Tool Shop played a decisive role in the construction of these machines. At that time, it was already equipped with planers, vertical milling machines, lathes, grinders and drills. The production of single-purpose machines increases the number of toolmakers to 35 workers.
More information about the Tool Shop can be found in the “Description of the Laurin & Klement Factory” from 1920. The Tool Shop with already fifty machines, connected with a warehouse and a Tool dispensary, produces not only drilling templates and turning knives but also a number of items of special tools and accessories. In addition to this assortment, the Tool Shop produces prototype parts for cars, spare parts for racing machines and practically everything for the further development of technology. There is also a description of the method of issuing a set of tools to production workers, where each tool had its own “baptismal certificate”, in which its movement and condition were monitored.
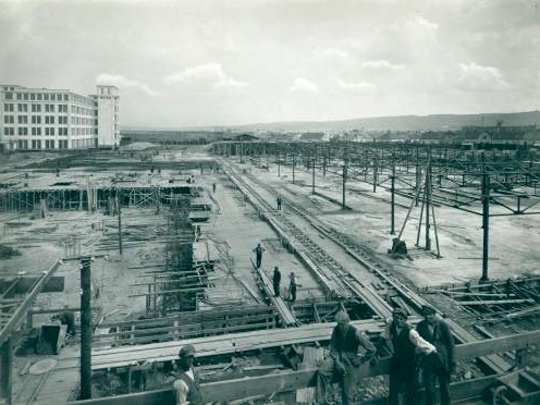
Construction of new mechanics
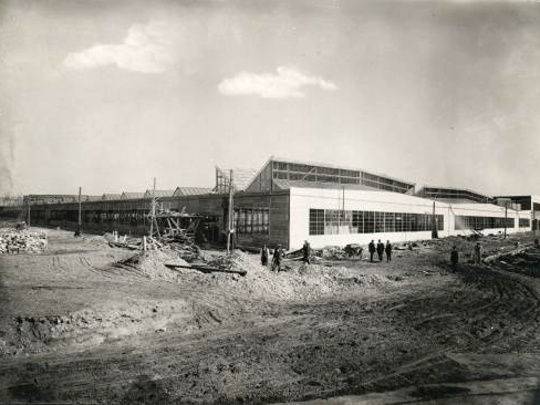
New mechanics before completion
In 1925 came a historical date that that strongly influenced the future of toolmaking – a connection with Plzeňská Škoda, which already had a strong toolmaking capacity at that time and owned what Boleslav did not have – a large press. In 1926, a new body shop (today’s apprenticeship centre) was completed, which also housed the assembly plant. An important role in the construction of the assembly plant was again played by the Tool Shop with its tools and jigs
An even more significant milestone was the year 1928, when a new mechanical hall, the so-called “AMERICA”, was built in an incredibly short period of time from April to December (the area of today’s polyclinic up to the training centre). A new Tool Shop with about 40 employees was also built here, while the Tool Shop in the old factory with 40 people existed for several more years and the records from that time speak of a new and old Tool Shop.
The year 1929 is the year of preparations for the launch of the Škoda 422. It is the first Škoda car to use sheet metal body moldings. And here is the historical period of the emergence of a completely new toolmaking discipline – the production of pressing tools, which at that time were called tensile dies. That is why a new department is created – the design of pressing tools. At that time, the nomenclature of some workshops also changed. In the minutes it is already written – the Tinsmith’s and Pressing’s Shop, for the production of tools – the Tool Shop.
In 1930, the car factory was renamed to the Joint-Stock Company for the Automotive Industry – ASAP and the car Škoda 422 was introduced to the public. The mouldings are pressed on a WEINGARTEN press in Pilsen with a pressing batch of 240 garnitures. These were the hood, lower covers, radiator grille, front and rear fenders, footrests, transverse walls, sills and headlight brackets. The mouldings were cut in Mladá Boleslav. Large flat parts, such as doors, sides and roofs, continued to be produced in Boleslav by manual hammering on wooden knock-out mock-ups in a Tinsmith’s Shop. Tools for the production of chassis parts were in charge of an old Tool Shop, where jigs for the production of gears, non-serial spare parts and tools for milling machines, drills, turret lathes, automatic machines and grinders were created. On June 30, 1931, the Mladá Boleslav car manufacturer had a total of 214 machines and 105 employees in its two Tool Shops.
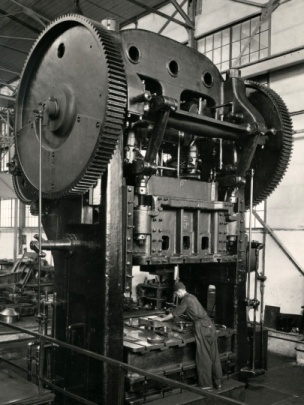
Car body press
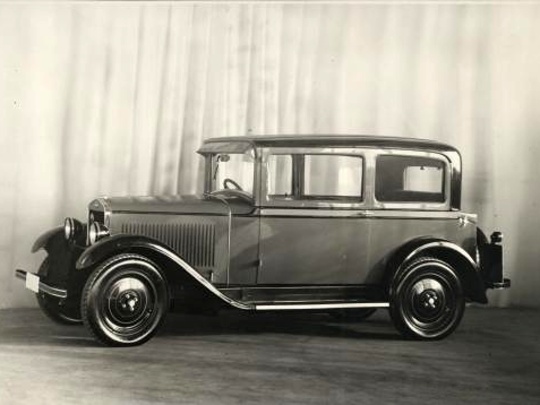
Škoda 422
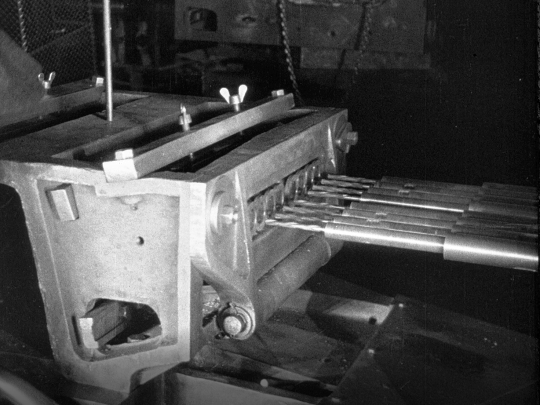
Cylinder head drilling
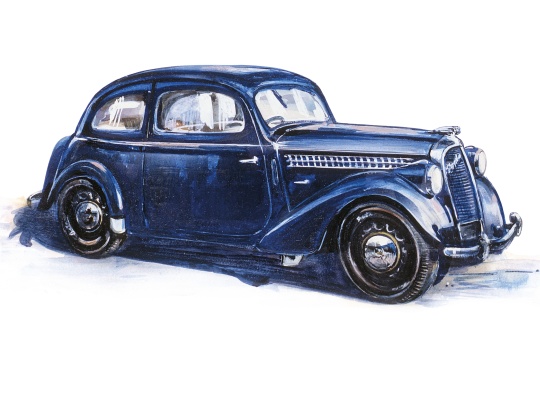
Škoda Popular 1100 OHV
In 1934, the Škoda Popular type was launched on the market with a split front and rear axle with a four-cylinder engine with SV valve train, later OHV. The concept and overall design of the Škoda Popular brought the Mladá Boleslav car manufacturer to the top of the production charts. The Škoda Popular meant another significant modernization of the production of car bodies and with it a further development of tool production. In August 1932, the company purchased 30 modern machine tools for a Tool Shop in America. In the following year, a new press was purchased to draw large mouldings.
After the war, in 1945, the company fell under the Československé závody kovodělné a strojírenské (ČZKS), from where the production program was ordered. It was decided that the small passenger cars would be produced exclusively by the Mladá Boleslav car manufacturer. The basis was the Škoda Popular type, which, after minor modifications, was given the type designation Škoda 1101. Its car body continued to be mixed, i.e. with a wooden skeleton to which sheet metal surface parts were attached. Press tools were still not widely used and the proportion of manual work remains considerable. Switching to all-metal car bodies would mean buying expensive technology, especially tools and large presses. The number of all passenger cars produced was in the thousands.
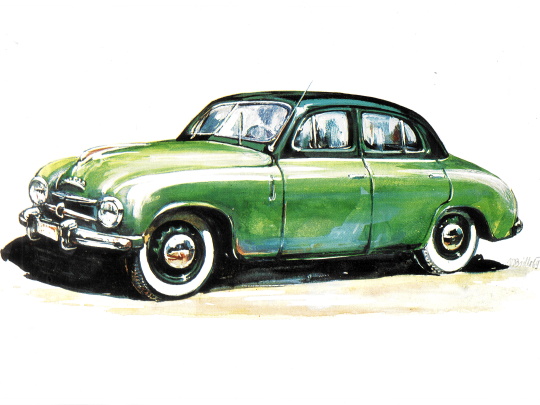
Škoda 1200
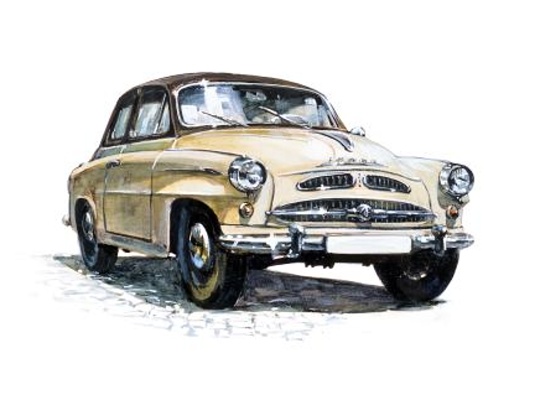
Škoda 440 Spartak
In 1946, the car manufacturer, called Automobilové závody národní podnik – AZNP, had four Tool Shops. The best equipped was the one in mechanics, where complex jigs, cutting tools, templates, gauges and dies for smaller mouldings and seals were created. The Tool Shop of the Tinsmith’s Shop produced pressing and welding tools. There was also a gas furnace for hardening. In the third Tool Shop, in building 109, the first two-draw press was built for finishing of pressing tools. The first castings of pressing tools with manual finishing of surfaces were also treated on machine tools. The fourth small Tool Shop was located in the Body Shop. It was used by upholsterers and templates for woodworking and spare parts for local machinery were also produced here.
In 1949, despite the American embargo, the Tool Shop was able to acquire the then top-of-the-line Keller copying milling machine. This marked the beginning of the era of pressing tool production by machining shaped surfaces using the copying method according to wooden and plaster mock-ups. There were a number of complications associated with this – the wooden mock-ups of surface parts were deformed and the plaster mock-ups were increasing in volume. Even the supplied sheet metal was not suitable for forming. After this experience, the technology of production of pressing tools for the new Škoda 440 Spartak model was optimized. The surface parts were divided into several mouldings, which were then welded. For example, the front fender was divided into 4 parts. On the other hand, the more easily pressable parts were connected in pairs – the left and right rear fenders, or the bonnet and tailgate. This increased the productivity of the Press Shop. The problems with the production of tools are best characterized by the fact that the first assembled and fitted Škoda Spartak body had dimensional inaccuracies compared to the drawings. The start of serial production in 1955 was then associated with great labour in the modification of mouldings and also in the welding shop. In the same year, the Tool Shop produced the first automatic machining line in Czechoslovakia. The line is exhibited at the Brno trade fair and is intended for machining cylinder heads. Along with the growing production of vehicles, cooperation with external companies in the production of tools is also growing. Especially in the production of casting models, it allows you to keep the supply of tools at the planned level.
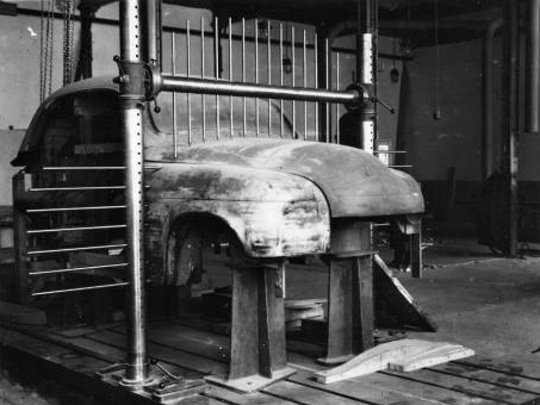
Škoda 1200 model on a measuring jig
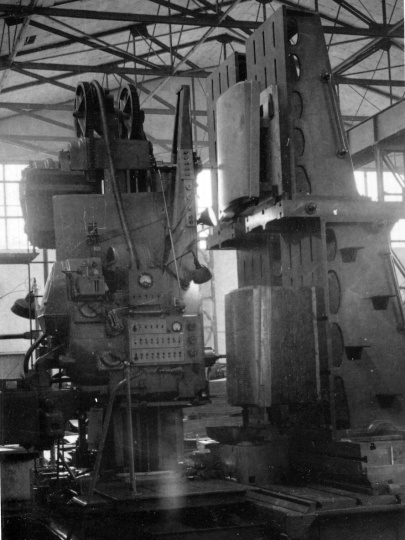
Keller copy milling machine
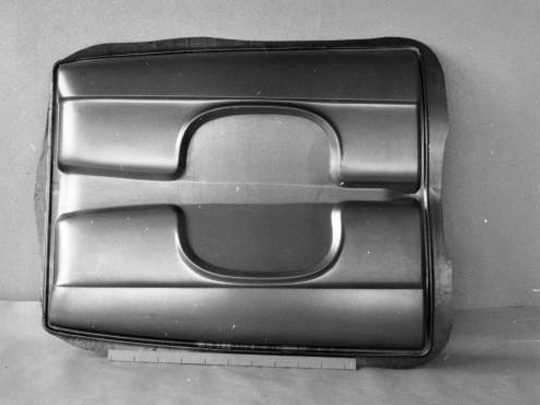
Together molded right and left fender
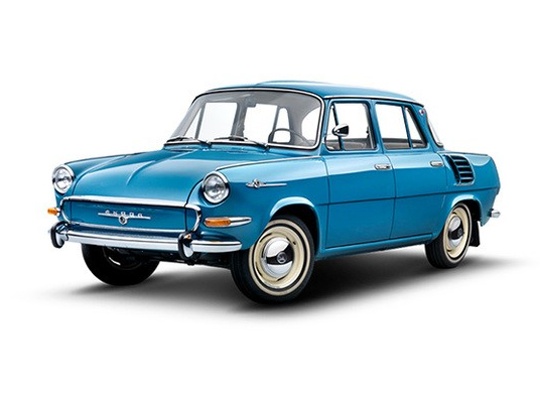
Škoda 1000 MB
One of the car manufacturer’s other milestones was the period from 1960. . During the production inspection for the upcoming Škoda 1000 MB, it turned out that the current method of casting the engine block and gearbox using the classic method of aluminium is too time-consuming. The ideal solution was to cast aluminum blocks under pressure into steel molds. This technology had a long tradition in Czechoslovakia. It was thanks to Ing. Josef Polák, who was granted a patent for this method in 1927. To die cast such a complicated semi-finished product, a metallurgical line had to be built, on which 59 different components were then cast in this way. Škoda was the first in Europe to use die-casting technology. In July 1961, an independent Department of Tools was established and the frantic design and production of moulds and jigs began, as well as the frantic purchase of technology and demand for cooperating companies. Immediately after the launch of the Škoda 1000 MB in 1964, the company’s management mainly dealt with the need for renewal of special tools to maintain production according to the field of industry. That is why 3 separate operations were established under the tools manufacturing:
Production of metallurgical tools (production of die-casting moulds for engine blocks and gearbox housings)
Production of pressing tools (tools for sheet metal pressing)
Production of welding tools and Jigs (welding tools for car bodie welding)
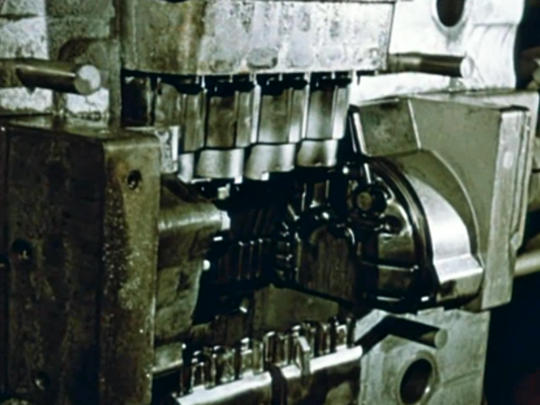
Mold for aluminum die casting
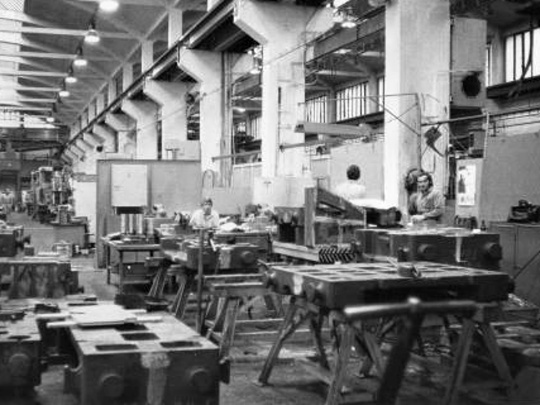
Production of pressing tools on
Škoda 1000 MB
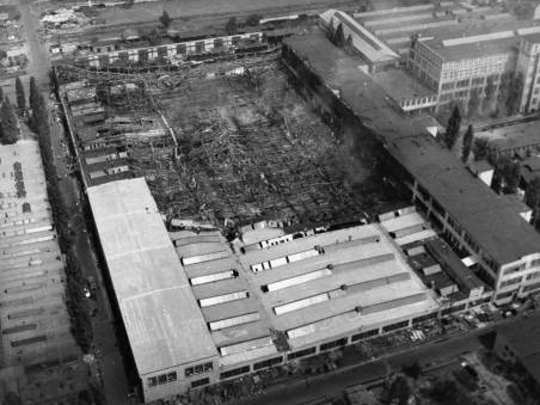
Mechanics fire 1969
In 1965 there was a change in the production of die models. Recently, they have been made of expanded polystyrene. The finished models are covered with sand in specially prepared moulds in the Foundry and poured with molten cast iron. Polystyrene will burn and be replaced by cast iron. After cooling, the finished casting is returned to the Tool Shop. Here it is machined and incorporated into the final form of pressing tools, which are used in press shops for pressing body parts. In 1967, the Tool Shop began producing special tools for the production of Škoda 100/110 cars.
The situation was complicated by the fire of object 109 (mechanics) in August 1969, which destroyed a large part of the Tool Shop – maschining area. As a result, the Tool Shop lost its premises, but also its machines.
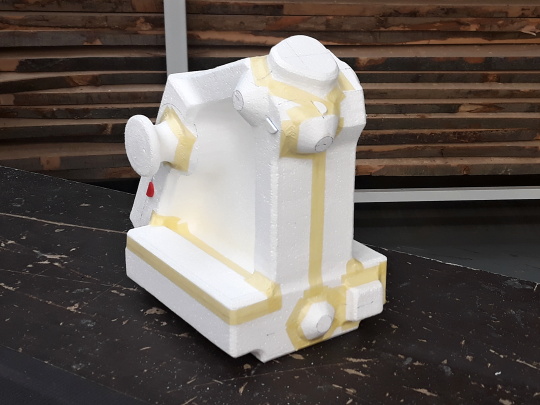
Polystyrene model
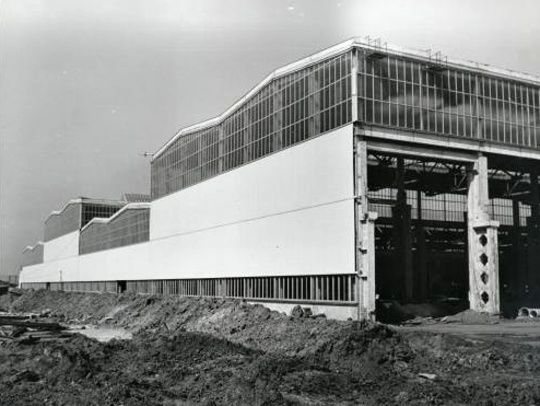
Construction of hall V17
At the beginning of the 1970s, preparations for the production of special tools for Škoda 105/120 series cars began. The Tool Shop then produces most of the pressing tools for these modernized Škoda cars. At the same time, the construction of hall V17 began, where the individual tool production facilities were gradually relocated until its completion in 1985. In connection with the production of tools for the Škoda Favorit/Forman series, modern electrochemical and electroerosive digging machines were purchased. Changes have also come to the tool design department. Since time immemorial, only work has been done on the drawing board and with mock-ups. Now the design and production with the support of CAD/CAM programs has begun. In construction, they had to learn how to create drawings and spatial models in special programs on computers.
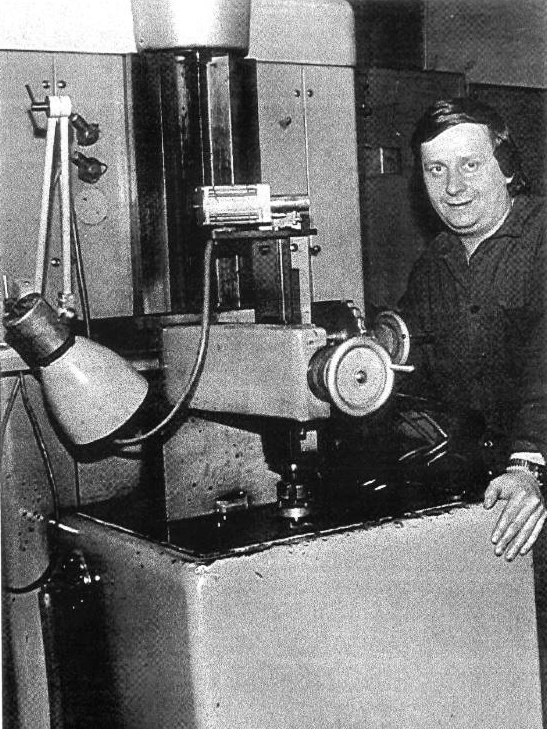
EDM machine
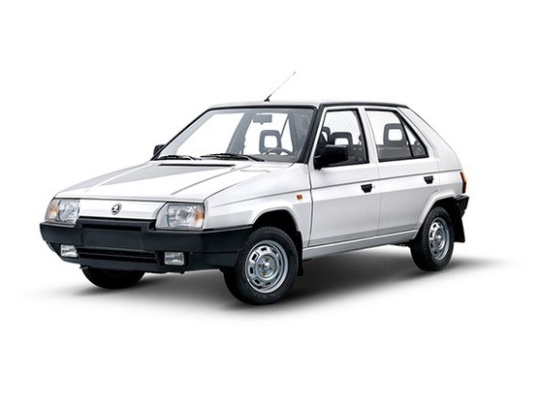
Škoda Favorit
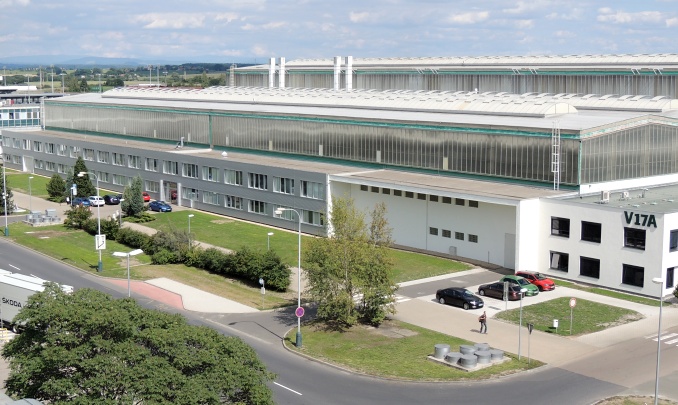
Hall V17 – tool shop
Perhaps the most important milestone in the company’s history was the agreement on the entry of the VW Group into AZNP, which took place on April 16, 1991. The VW Group has acquired a conceptually good product and an experienced, high-quality staff of workers, but an outdated factory with technology that in many cases was not only a brake on further development, but sometimes also represented an environmental danger. It was necessary to start the construction of new operations and introduce modern technologies, innovations and know-how.
With the preparation of the production of the new Škoda Felicia in 1992, the Tool Shop continued to switch from production according to mock-ups to production according to data (development of CAD/CAM technologies). All this big change was conditioned by investments in computer technology. The design offices were gradually equipped with computer stations with CAD software CatiaV3, Euclid and Autocad. New programmers’ workplaces equipped with CAD/CAM programs were built.
CNC machine tools began to be introduced into production. The training of CNC machine operators took place on the so-called school CNC milling machine from the German company Droop & Rein. At the same time, the construction of the machining line began, which consisted of two FPV 2200 rough CNC machines, one FOG CNC machine for finishing machining, and a DEA coordinate measuring machine. Part of the line was a pallet system that allowed the workpiece to be set, measured and placed in the required machine.
In 1996, the Tool Shop was awarded the EN ISO 9001 certificate – quality management system. These standards make it possible to demonstrate the ability to manufacture and distribute an organization’s products in accordance with regulations and customer needs. With the introduction of new methods, the preparation of tool production has been accelerated. These were simulation programs for the simulation of sheet metal drawing “AUTOFORM”, kinematics of pressing tools “dCade”, improvement of the quality of pressings thanks to the use of CAD/CAM technologies. Cooperation with other Tool Shops of the VW Group has also developed.
Since 1997, the tool shop of the automobile company has been officially included among the recommended European manufacturers of tools for the production of dies for all surface parts of car bodies. The Tool shop Škoda joined the Association of Tool Shops, which participates in the dynamic development of Czech toolmaking companies.
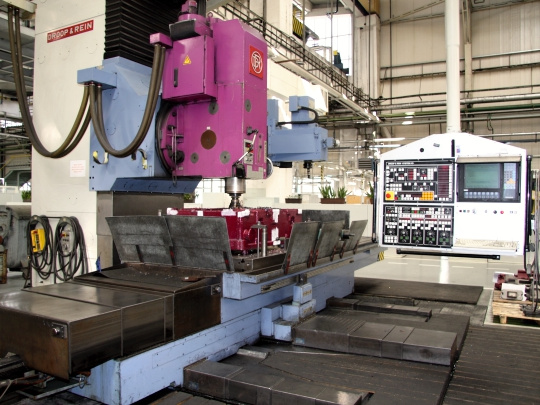
School milling machine Droop & Rein
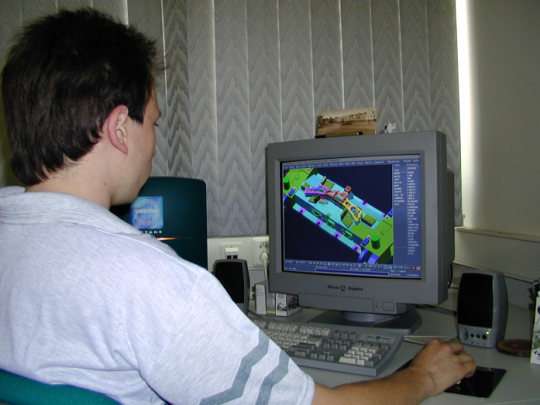
CAD SW Catia
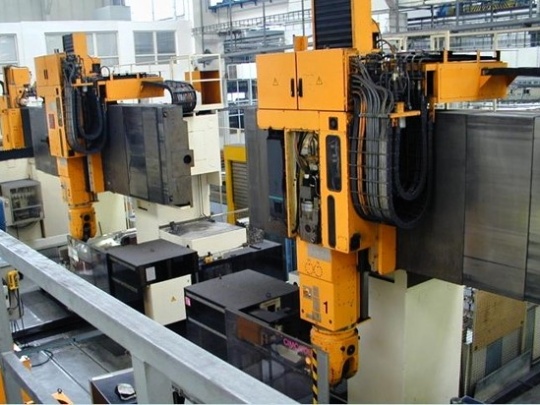
Droop & Rein machining line
Join our team
You can find vacancies on the skoda-career.com portal. Please contact our specialists.